
With some TLC and truss rod / bridge adjustments we were able to fix the fret buzzing and set up the guitar with the right action and intonation tuned to D Standard. We were pleased that when we plugged the guitar in for the first time there were no electronics issues with minimum fret buzzing. After some light sanding we added a base coat of blue metallic paint with a clear coat of lacquer. We painted the guitar with a coat of plastic primer followed by a coat of high build primer. In that time we had to paint, finish the electronics and cut the Queensland Mahogany to insert into the body of the guitar. We had 6 days to finish the guitar before we had to leave Adelaide to go to Melbourne to showcase our guitar for National Manufacturers week. Having personally made a 1959 Gibson Les Paul replica from scratch we have found printing the shell of the body out of PLA with a Queensland Mahogany block dramatically streamlined the process of making the body.
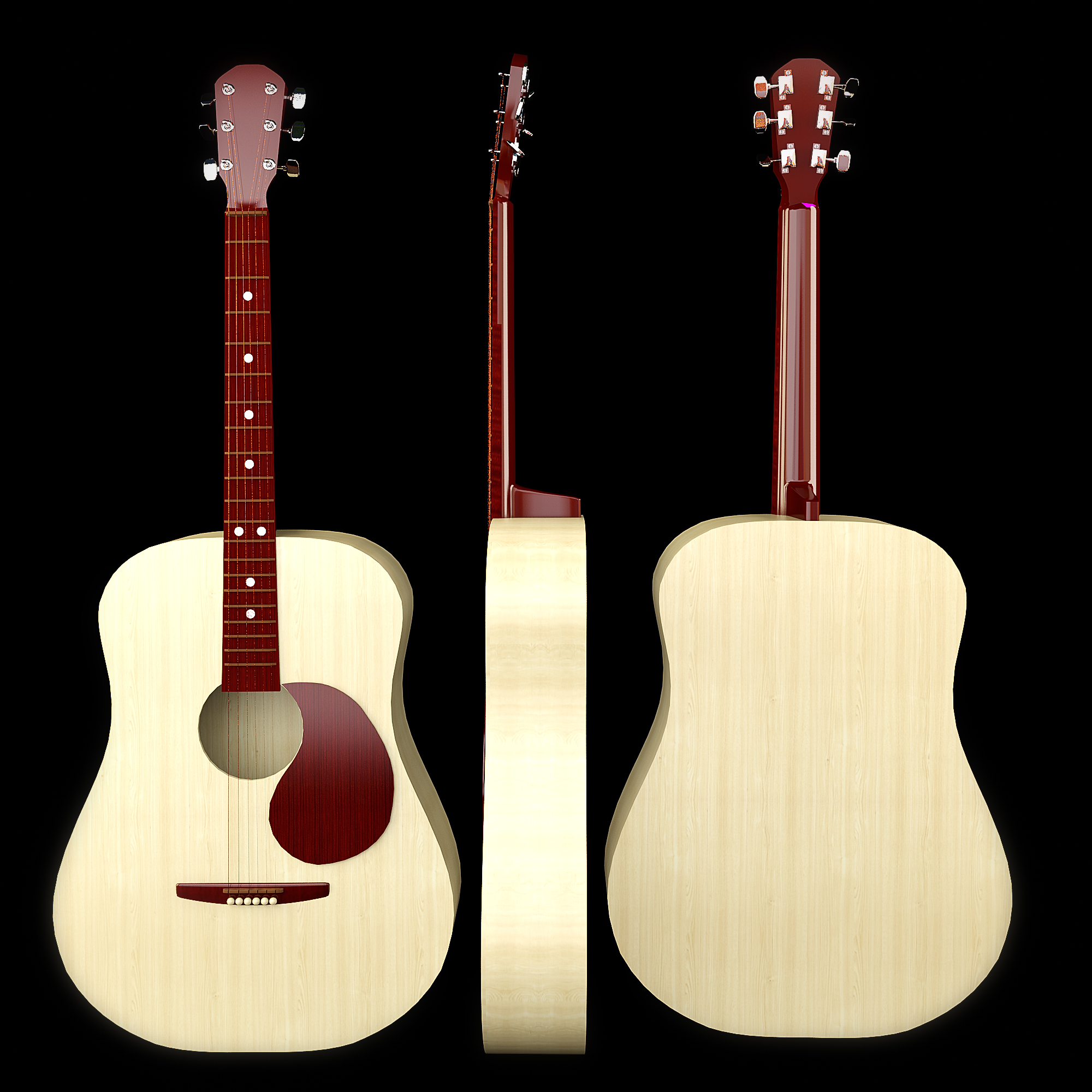
In addition we have designed the guitar so you can easily change to different 3D Printed Bodies in under 45 minutes. The playing card suite design is a good example of this. By using FormZ and 3D Printing we were able to add designs to the body which would be difficult with conventional wood working techniques. We find FormZ really easy to use and it exports to perfect stl files ready for your 3D Printer. To create the 3D Design we used FormZ 3D Design Software. This guitar is a hybrid of the latest 3D Printing Technologies with traditional Guitar Luthier techniques, utilizing a maple neck and mahogany block fitted in the body to provide traditional tonal qualities.
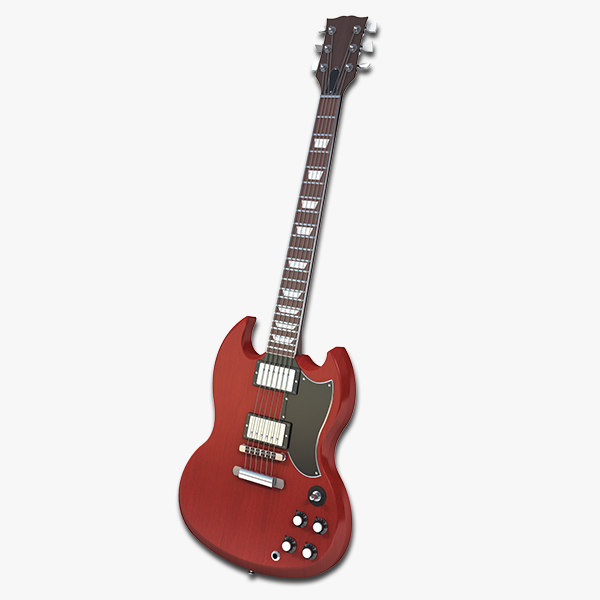
The project was successful due to the combination 3D Design skills by Michael Tyson and some helpful advice from myself. The body was designed and printed in four parts on the new UP Box 3D Printer using a unique PLA filament called PolyMax PLA, due to its high strength and resistance to warping.
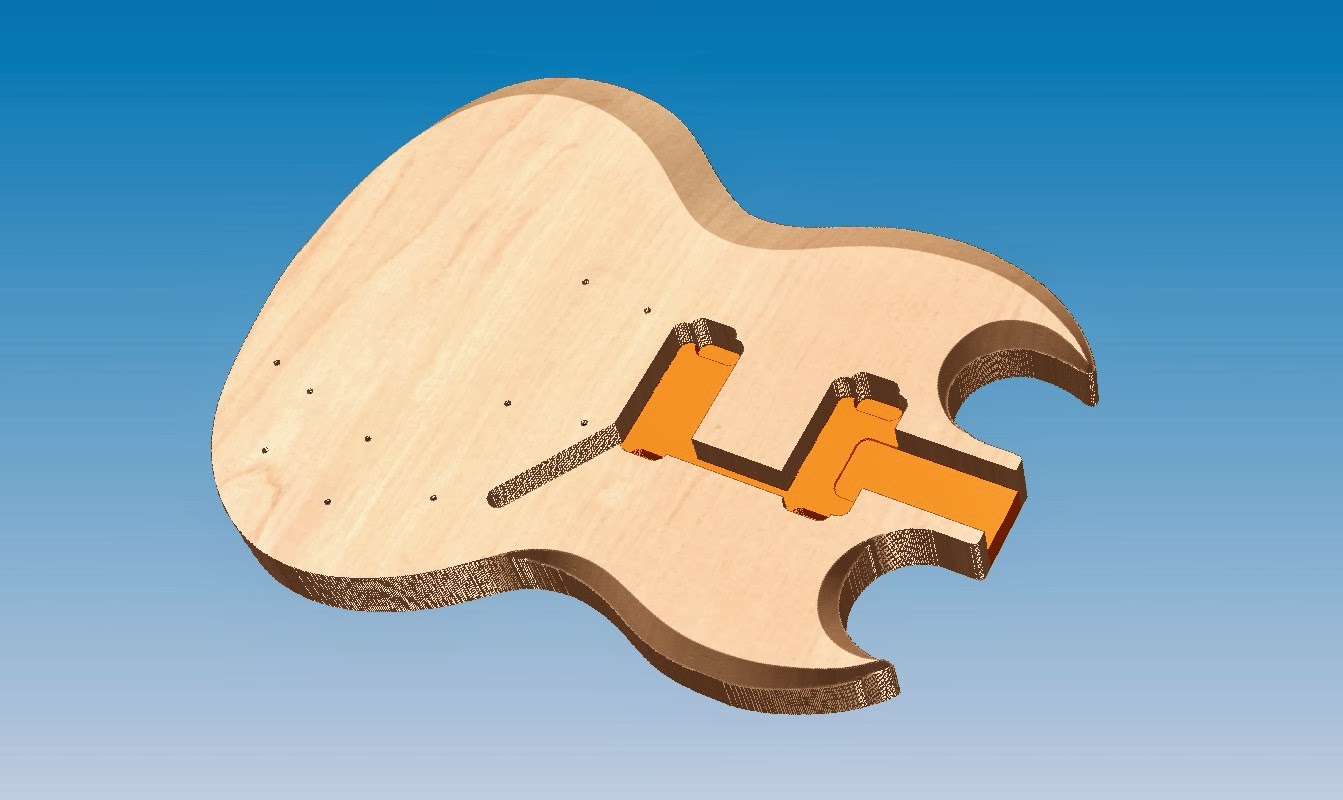
The first thing that came to mind was a 3D Printed Guitar! When the UP Box was first announced our CEO Michael Tyson knew we had to find a project that would utilise the larger build area of this new 3D Printer.
